Le fabbriche Intel in Malesia: come assembly e packaging trasformano un wafer in un chip
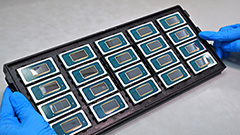
Le fasi di produzione di un moderno processore vengono sviluppate all'interno di varie sedi, ciascuna specializzata in una serie di operazioni fondamentali per il risultato finale. Quelle in Malesia di Intel operano nell'assemblaggio, nel packaging e nel test dei prodotti: siamo andati a vedere come un wafer in silicio viene lavorato per ottenere il prodotto finale, la CPU.
di Paolo Corsini pubblicato il 27 Novembre 2023 nel canale ProcessoriIntel
Il ritorno di Pat Gelsinger in qualità di nuovo CEO di Intel, avvenuto nei primi mesi del 2021, ha visto l'azienda proiettarsi all'interno di quella che è una strategia molto differente rispetto al passato. IDM 2.0 è il nome che la definisce: mette al centro la capacità produttiva di Intel, che viene sempre più rivolta non solo al soddisfare la costruzione di chip proprietari ma anche soluzioni per conto di clienti terzi.
5 nuovi processi produttivi in 4 anni: questa l'ambiziosa roadmap interna di Intel
Intel, in questo modo, vuole competere direttamente con aziende del calibro di TSMC e Samsung, rilanciando la produzione di semiconduttori in aree del globo che sono lontane dall'Asia e in questo modo seguire meglio i propri clienti. Un approccio che porta a una radicale riorganizzazione interna all'azienda, con investimenti a dir poco ingenti richiesti per l'espansione delle fabbriche attive al momento oltre che per la costruzione di nuove sedi produttive.
In quest'ottica dobbiamo rimarcare l'annuncio legato alla costruzione di una nuova fabbrica produttiva a Magdeburgo, in Germania, per la quale è stato preventivato un costo di oltre 30 miliardi di dollari e inizio della produzione di chip previsto per il 2027. Non è questa l'unico investimento che Intel ha in programma per i prossimi anni in Europa, dove del resto già ha una sede produttiva in Irlanda: molto si discute se questo potrà riguardare anche il nostro Paese con una sede dedicata alle operazioni di packaging.
Wafer da 300mm contenente die di processori Meteor Lake
Al momento, Intel produce wafer in Oregon, Arizona, Ohio, Irlanda e Israele con la citata futura fabbrica in Germania per la quale verrà avviata prossimamente la costruzione. Le operazioni di Advanced Packaging vengono svolte in New Mexico e in Malesia, mentre quelle di Assembly e Testing sono concentrate in Costa Rica e Vietnam, a Chendu in Cina e nuovamente in Malesia con una nuova sede prevista in Polonia e che verrà costruita nei prossimi anni.
Ho avuto occasione di visitare il polo produttivo Intel in Malesia, suddiviso tra le località di Penang e Kulim, all'interno del quale l'azienda americana svolge molte attività legate alla produzione dei propri chip. Quello che avviene in Malesia è legato a tutte le fasi che seguono la costruzione di un wafer, cioè del disco in silicio all'interno dei quali sono presenti i vari chip e che molte volte abbiamo visto in immagini scattate all'interno di una fabbrica produttiva.
la produzione dei semiconduttori passa attraverso molte fasi
Nell'immaginario collettivo queste fasi possono sembrare essere marginali rispetto a quelle di costruzione del wafer, ma non c'è nulla di più sbagliato. Si è arrivati addirittura a pensare che una di queste fasi, quella del packaging, fosse quella dell'inscatolamento del prodotto nella confezione di vendita (traducendo in modo letterale l'inglese packaging) quando è emersa l'intenzione di Intel di aprire una propria fabbrica in Italia per il packaging dei prodotti: meriti della stampa generalista.
Dobbiamo pensare a queste semplificazioni con il sorriso sulle labbra: al momento attuale le attività di packaging dei prodotti sviluppati da Intel sono così sofisticate ed elaborate da poter essere equiparate per complessità alla stessa produzione dei wafer. Interessano chip sviluppati con tecnologie produttive molto diverse tra di loro e in alcuni casi abbinando prodotti costruiti da Intel con altre di fonderie terze.
In Malesia Intel è presente dal 1972, con una forza lavoro che al momento attuale tocca le 15.000 unità. Nelle sedi di Penang e Kulim Intel svolge diverse attività: parliamo di assembly e test, die sort, die preparation e packaging. Sono tutte lavorazioni che interessano, come punto di partenza, un wafer di silicio proveniente da una delle fabbriche produttive dell'azienda e che portano come risultato alla creazione del prodotto finale. Poco importa cosa questo sia: un tradizionale processore x86, un acceleratore di qualche tipo o una delle GPU utilizzate sia nei prodotti consumer come all'interno dei grandi datacenter. Per tutti questi prodotti il lavoro svolto in Malesia è fondamentale per il risultato finale.
Oltre a questo Intel sviluppa in Malesia tutti i macchinari che l'azienda utilizza per i propri test interni sui prodotti che vengono costruiti: si tratta infatti di soluzioni custom, sviluppate e perfezionate nel corso degli anni da Intel così da facilitare e migliorare la produzione dei componenti che andranno poi venduti sul mercato.
Il wafer entra in fabbrica
Sappiamo che il processo di costruzione di un moderno chip prevede la creazione, all'interno di fabbriche dedicate, dei wafer: si tratta dei ben noti dischi, da 200 o 300 millimetri di diametro a seconda del tipo di fabbrica coinvolta nella loro produzione, che integrano al proprio interno un numero variabile di chip tutti costruiti uno accanto all'altro. In un singolo wafer è presente un numero variabile di chip: questo dipende dalla loro tipologia, quindi dal numero di transistor in essi integrati, dalla tecnologia produttiva adottata per la loro costruzione e dalla superficie complessiva che occupano.
Wafer pronti per iniziare il processo di lavorazione
Una volta costruiti i wafer vengono inviati in altre fabbriche, come quelle malesi, per trasformare i singoli chip in prodotti destinati ai clienti. I wafer entrano nella fabbrica interi e in essa vengono processati attaccandoli a una sottile pellicola adesiva di Mylar: questo materiale è scelto perché ha proprietà adesive quando non toccato da raggi ultravioletti. Operando in un ambiente dove l'illuminazione non prevede questo tipo di sorgente luminosa i singoli chip ottenuti dal wafer restano attaccati alla pellicola, facilitando il loro trasporto da una stazione all'altra almeno sino a quando non dovranno poi essere staccati.
I wafer sono dischi da 200mm o 300mm nei quali si trovano molti chip identici
Un wafer, come detto, contiene chip tutti uguali con specifiche caratteristiche tecniche: una ben definita tecnologia produttiva, un numero di transistor che si concretizzano poi in un determinato quantitativo di core e dimensione di cache. Non tutti i chip di un wafer si comportano però in modo identico tra di loro: alcuni possono avere dei transistor difettosi, che portano a disabilitare alcune funzionalità (meno core attivi o una cache totale più piccola, ad esempio), altri possono avere un comportamento migliore o peggiore in termini di frequenza di clock massima.
È per questo motivo che esistono diverse tipologie di processori, identici per numero di core e caratteristiche tecniche ma magari differenti per le frequenze di funzionamento massime. In questo modo non solo Intel ma tutti i produttori di chip riescono a massimizzare il rendimento di ogni wafer, quindi a sfruttare il maggior numero possibile di chip a disposizione. Tutta la fase di testing dei prodotti che avviene all'interno delle fabbriche è necessaria per verificare non solo il corretto funzionamento di questi componenti, ma anche per capire quali saranno le caratteristiche finali e quindi in quale specifica soluzione commerciale verranno utilizzati.
Taglio del wafer per separare i singoli die
I die sono tutti attaccati tra di loro quando sono presenti nel wafer; per ottenere il singolo chip i wafer passano attraverso il cosiddetto die separation, una serie di processi che utilizzano il laser per procedere a un taglio netto dei wafer. Un secondo processo prevede che delle lame con punta diamantata completino l'operazione di taglio del wafer, con un getto di acqua spruzzato nel punto di taglio così da raffreddare il wafer ed evitare che eventuali detriti si depositino sulla sua superficie.
Ove possibile le operazioni vengono tutte automatizzate
Questa operazione viene eseguita da una macchina automatizzata, che effettua un monitoraggio costante evitando che il taglio possa generare problemi a ogni die. A seguire, una nuova stazione procede a rimuovere i singoli die dal wafer, posizionandoli su una superficie uno affiancato all'altro così che possano procedere alle successive fasi di lavorazione.
I singoli die dopo essere stati tagliati dal wafer
Da segnalare come alcuni die debbano passare attraverso un ulteriore processo di lavorazione: quelli destinati a dispositivi mobile, ad esempio, vengono leggermente assottigliati in quanto non verranno montati con un heatspreader superiore ma saranno posizionati a diretto contatto con il sistema di raffreddamento integrato nello specifico dispositivo (PC o notebook che sia).
Ogni chip viene testato
Abbiamo detto che ogni wafer contiene chip, o die, che sono identici tra di loro quanto a caratteristiche tecniche. In realtà il loro comportamento differisce in quanto alcuni possono avere componenti non funzionanti, o riuscire a operare a frequenze di clock più elevate in base all'alimentazione fornita.
Una delle unità di testing dei chip interna alla fabbrica
I sistemi di testing interno ricevono i chip da sistemi autonomi che li muovono da una parte all'altra della fabbrica
Per capire quali caratteristiche abbia uno specifico chip e quindi per quale prodotto possa venir adattato, Intel procede a un'operazione di test specifico: si tratta di un sistema costruito dall'azienda stessa, composto da 20 unità di testing ciascuna, del quale sono presenti svariate centinata di unità all'interno della fabbrica malese.
Ogni cella di test opera in modo completamente indipendente dalle altre: riceve una serie di chip da robot che li prelevano da un magazzino interno, li testano singolarmente e li riportano a destinazione con la specifica identificazione delle proprietà e quindi di quale tipologia di prodotto commerciale sarà possibile costruire con essi.
Particolare di una scheda di test: a seconda del prodotto da testare viene sostituita con altre
Tutto il processo di testing di ogni die viene svolto in modo completamente automatizzato all'interno della fabbrica: non c'è intervento da parte degli addetti, se non quello di monitorare il corretto funzionamento e intervenire qualora qualcosa non si svolga in modo corretto. Lungo i corridoi di questa parte della fabbrica si muovono gli AGV, Automated Guidance Vehicles, che prelevano i chip portandoli a ogni unità di test e che li riprendono una volta completata l'analisi, riportandoli in magazzino.
Lunghi corridoi di sistemi di test dei chip completamente automatizzati
Una volta caratterizzate le proprietà di ciascun die, i chip vengono montati su rulli che ricordano le pellicole cinematografiche, fissati da due strati di pellicola posti sopra e sotto: in questo modo saranno poi spostati lungo le altre fasi del processo di lavorazione, passando a quella di assemblaggio che si solve in altra fabbrica Intel distante alcuni chilometri.
Una volta tagliati e testati i chip vengono montati in questi rulli per essere trasportati
Il packaging: no, non parliamo di scatole
L'evoluzione dei moderni processori vede la costruzione di prodotti sempre più sofisticati, che in alcuni caso vedono l'abbinamento di chip diversi sullo stesso prodotto. Questi chip possono essere sviluppati in fabbriche diverse, anche da aziende differenti e di conseguenza con tecnologie produttive che variano volta per volta.
Alcuni esempi di prodotti Intel con advanced packaging: Sapphire Rapids, Meteor Lake e Ponte Vecchio
È nella fabbrica PG8 di Penang che Intel attua la fase di Advanced Packaging, prendendo i diversi die e abbinandoli sul substrato corrispondente. In alcuni caso la complessità costruttiva è così elevata che possono essere montati ben 12 diversi chip sul package, come nel caso della GPU Intel Ponte Vecchio destinata alle elaborazioni parallele in datacenter.
L'advanced packaging è una delle fasi di costruzione di un moderno chip a più elevata complessità
Ogni chip è dotato di centinaia o migliaia punti di contatto con il package sul quale viene montato: ognuno di questi collegamenti, fisicamente molto piccoli, deve essere ovviamente correttamente posizionato affinché il prodotto posa operare correttamente. Intel ha sviluppato nel corso degli anni tecnologie specifiche per il packaging, come quella Foveros utilizzata in vari prodotti da alcuni anni.
GPU Ponte Vecchio prima (destra) e dopo (sinistra) essere state trattate con materiale epossidico
Una volta che i singoli chip vengono posizionati e i collegamenti con il substrato, viene applicato un sottile strato di materiale epossidico così da migliorare la stabilità del prodotto. In seguito viene fissato l'heatspreader, la placca in metallo che copre la parte superiore del chip posta a diretto contatto con i vari die così da proteggerli e fungere da strato intermedio tra i die e il sistema di raffreddamento adottato. Questo non vale tipicamente per i processori destinati ai sistemi mobile e ai notebook, per i quali il die viene lasciato esposto così da entrare a diretto contatto con il sistema di raffreddamento riducendone lo spessore complessivo.
Processori della famiglia Meteor Lake pronti per essere testati
Tra die e heatspreader viene posto, ovviamente con una procedura automatizzata, del TIM o Thermal Interface Material: si tratta di quella che viene tipicamente indicata come pasta termoconduttiva, che gli appassionati stendono sopra l'heatspreader del processore quando posto a diretto contatto con il sistema di raffreddamento in un PC desktop.
Alla fine un ultimo test
Ogni die prodotto viene testato, come segnalato in precedenza, prima che venga preso e montato sul substrato corrispondente così da dare vita al prodotto finale. Una volta completata l'operazione di packaging il prodotto finale viene testato nuovamente all'interno del Design and Development Lab.
File di sistemi di test con le configurazioni più disparate per testare i prodotti pronti per la commercializzazione
Il test finale passa su sistemi identici a quelli in commercio che eseguono moltissime applicazioni
In quest'area della struttura sono presenti svariate file di sistemi che permettono di testare tutti i prodotti con differenti tipologie di test, a partire da quelli di burn-in che portano i chip a operare a temperature e tensioni di alimentazione elevate così da verificare la presenza di eventuali difetti di funzionamento. Completata questa fase si passa a un'analisi dettagliata di tutti i segnali elettrici dei chip, alla ricerca di eventuali malfunzionamenti. Ultimo passaggio è quello legato all'utilizzo del prodotto in un ambiente di lavoro che replica quello nel quale sarà utilizzato dal cliente in produzione, coinvolgendo nell'analisi anche quei componenti del chip che interagiscono con altri presenti nel sistema: si pensi ad esempio alle schede PCI Express, o alla memoria collegata al controller integrato nel processore.
È interessante evidenziare come i sistemi che Intel utilizza per testare i propri prodotti una volta giunti al termine della fase di produzione sono a loro volta costruiti internamente all'azienda, seguendo una logica che da un lato spinge verso la modularità dall'altro cerca di fare in modo che un sistema di test possa essere facilmente riadattato al testing di differenti tipologie di prodotti.
Un chip difettoso viene studiato per capire quale sia il problema sul quale intervenire in produzione
Nel caso in cui un chip dovesse evidenziare dei malfunzionamenti, il Failure Analysis Lab (FAL) interno all'azienda procede ad analizzare il prodotto per capire quale ne sia la causa e come questo possa in qualche modo influenzare l'intera produzione. L'analisi viene condotta tipicamente in modo non invasivo, ad esempio usando uno scanner ultrasonico per analizzare le componenti interne oppure eseguendo verifiche con un microscopio per evidenziare eventuali problemi nei punti di contatto tra die e substrato.
Il packaging del futuro sarà in Italia?
Dovremmo ormai averlo capito: il packaging dei processori non è la fase che li inserisce, una volta costruiti, all'interno di una bella confezione di cartone ma una delle fasi più sofisticare legate alla sua produzione. Intel deve aprire una sede produttiva legata a queste operazioni in Europa, così da fornire supporto alle sedi di produzione dei wafer in Germania e di Assembly e Testing della Polonia che ha annunciato negli scorsi mesi. L'Italia è una delle nazioni candidate: una sede produttiva di questo tipo porterebbe una tra le lavorazioni tecnologiche più sofisticate nel nostro tessuto produttivo, con tutte le ricadute in termini di occupazione, sviluppo e indotto. Diciamolo chiaramente: è un'opportunità che va assolutamente colta.
Quello che avviene all'interno delle linee produttive Intel in Malesia è dal punto di vista logico facile e intuitivo. I processi sono ben definiti e le lavorazioni che conducono al prodotto finale eseguite in sequenza, spesso con un notevolissimo livello di automazione. Quello che sorprende è la portata delle operazioni richieste e il costante equilibrio tra le fasi che permette di avere prodotti finali perfettamente funzionanti, pronti per essere forniti ai clienti finali.
Un nerd con alcuni miliardi di transistor tra le mani: l'immancabile foto ricordo di un'esperienza unica
Osservando solo parte della struttura produttiva di Intel in Malesia, cosa che di fatto per la prima volta l'azienda ha concesso di fare a un gruppo di giornalisti internazionali, si resta però sorpresi da quanto tutti questi processi automatizzati vedano moltissimi dipendenti Intel impegnati su vari fronti. L'interazione umana, pur con tutta l'attività di Intelligenza Artificiale che governa le operazioni e opera per massimizzare le rese produttive, rimane molto alta e ci porta a pensare che pure in una struttura così complessa il ruolo di operatori qualificati sia imprescindibile.
Ed è sempre affascinate osservare come anche la più sofisticata delle tecnologie, anche in tempi nei quali l'automazione sia spinta a livelli impensabili anni fa, richieda ancora una presenza di personale estremamente qualificato. Sono queste persone che, come un direttore con la propria orchestra, governano i tempi dei singoli esecutori facendo in modo che l'esecuzione sia perfetta. Tutto questo è quanto sta dietro alle centinaia di chip integrati all'interno di tutti i prodotti tecnologici che sono quotidianamente tra le nostre mani.
2 Commenti
Gli autori dei commenti, e non la redazione, sono responsabili dei contenuti da loro inseriti - infoI wafer sono semplicemente dei dischi di silicio nei quali attraverso processi cosiddetti litografici vengono creati più die identici, quindi da un wafer trattato con processi litografici si ricavano più chips ...
Dunque il titolo dell'articolo lo avrei scritto più correttamente
All'articolo io avrei aggiunto anche questo:
Nel caso dei processori, che vengono notoriamente prodotti di diverso tipo si pensi per esempio ai core Intel i3, i5, i7, i9 e che lavorano con diversi range di frequenze di clock, questi sono tutti i dentici nei wafer (per capirci sono tutti die che potenzialmente potrebbero essere tutti processori core i9 della medesima generazione) che poi vengono differenziati proprio a seguito dei test descritti nell'articolo sia in termini di frequenze di clock e sia in termini di core effettivamente operativi ed è nel processo di packaging che vengono disattivati alcuni core ...
Tutto questo perché i wafer di silicio vengono prodotti nel seguente modo:
Da un "germe" di silicio (immaginate un ""granello" piccolissimo di silicio), tramite la crescita epitassiale per diffusione di atomi di silicio vengono creati dei cilindri di silicio (in gergo carote), i wafer sono dunque le fette di un certo spessore ottenute affettando le carote di silicio, esattamente come si affettano i salami, la mortadella, i prosciutti e compagnia bella ...
La realizzazione dei wafer di silicio che ho descritto sommariamente (e utilizzando anche un gergo più comprensibile anche ai non addetti) viene effettuata in tale modo per garantire la massima perfezione del reticolo cristallino formato dagli atomi di silicio e va da se che in un wafer per come viene realizzato il reticolo è più perfetto al centro che ai bordi ... questa imperfezione va aumentando dal centro del wafer verso il suo bordo ed è questo che costringe la differenziazione dei processori di una medesima generazione, tanto per capirci i die dei processori core i9 con moltiplicatore sbloccato vengo ottenuti dai die al centro del wafer dove appunto la struttura cristallina è più perfetta e meno contaminata da presenza di altri atomi e ovviamente i core i3 della medesima generazione vengono creati dai die presenti nelle aree più vicine al bordo del wafer di silicio
Ovviamente questo articolo serve a chi non ha intrapreso un corso di studi in elettronica in cui si studia anche la specifica materia di tecnologia delle costruzioni elettroniche, ma così come è scritto il titolo chi non ha studiato elettronica interpreta che da un wafer si produce un chip (un processore) ...
Devi effettuare il login per poter commentare
Se non sei ancora registrato, puoi farlo attraverso questo form.
Se sei già registrato e loggato nel sito, puoi inserire il tuo commento.
Si tenga presente quanto letto nel regolamento, nel rispetto del "quieto vivere".